Komoly gonddal küzd a Moderna-vakcina gyártója
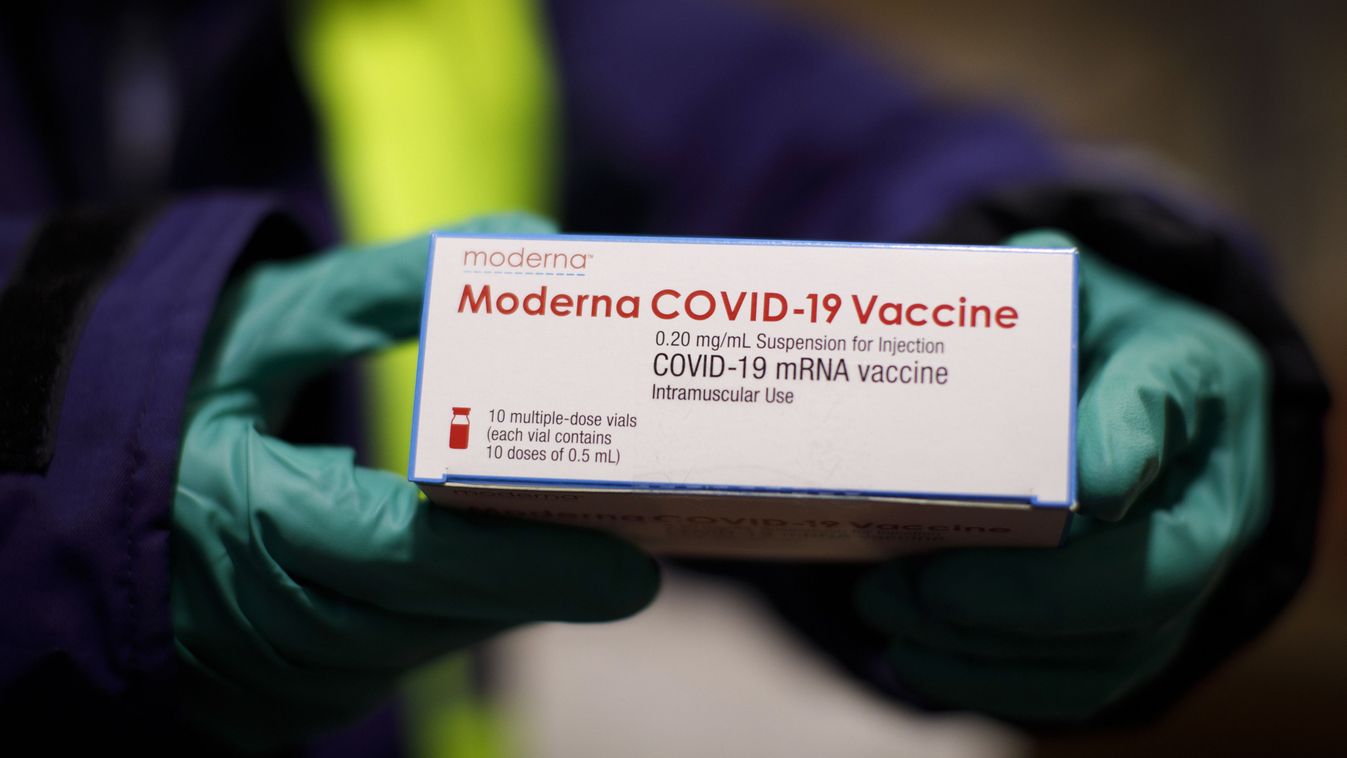
A COVID-19 vakcinák iránti csökkenő globális kereslet irányváltásra kényszeríti a céget.
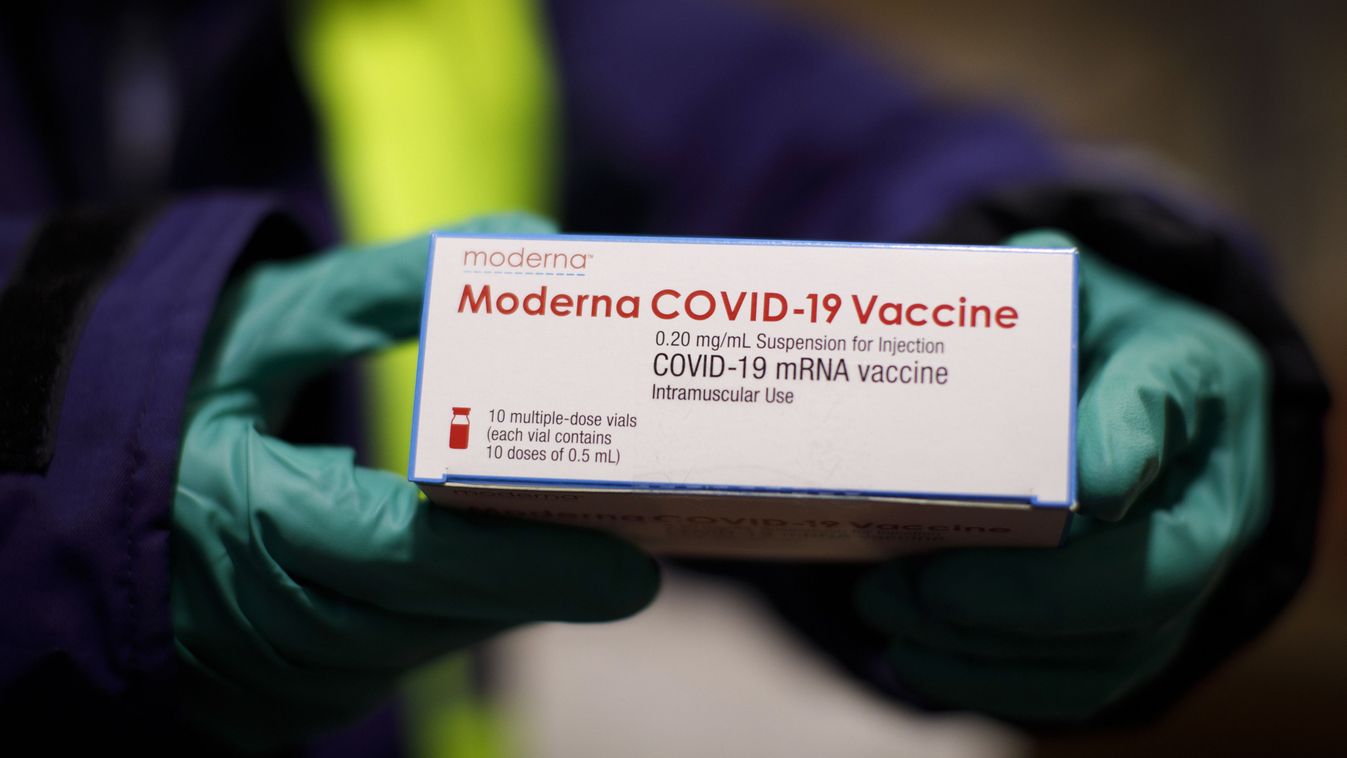
“To make your manufacturing lines more efficient and to extract labor, you have to move towards an automated solution. This makes manufacturing competitive in high-cost areas like America. It is one of the critical underpinnings of reshoring and looking at where in the world you should be manufacturing.” – Rosemary Coates, founder and Executive Director of the Reshoring Institute in a conversation with Lénárd Sándor.
As the Executive Director of the Reshoring Institute of United States, can you tell us the origin and mission of this organization?
Ironically, I spent around 15 years in management consulting helping companies offshore to China. During the 2012 Presidential election, both candidates (Barack Obama and Mitt Romney) had aversion to offshoring to China. They both emphasized that it was China's fault that we were struggling with high unemployment rates and we were experiencing economic downturns. As I was helping a lot of companies offshore to China, it was a bit embarrassing and I felt uncomfortable that I was still doing this. At the same time, a few of my clients were interested in potentially bringing their manufacturing back to the U.S. So I got my team together to develop a methodology for evaluating the total cost of ownership (TCO) model and how companies might make a decision to bring manufacturing back to the U.S. This kind of evaluation is a global manufacturing strategy determination in terms of where in the world companies should be manufacturing.
Reshoring does not mean ripping everything out of China or making a complete about-turn and bring everything back.
That is not the way the world works anymore. Instead, it is the idea of setting up manufacturing in multiple locations and multiple countries.
Out of this analysis and methodology, the Reshoring Institute was created. We were originally affiliated with the University of San Diego and now we have affiliations with about 15 universities across America including some of the big names universities and engineering schools. The Reshoring Institute has two missions. The first mission is to help clients evaluate their global manufacturing strategies what they could bring back to the U.S. Our second mission is to train graduate student interns about the manufacturing world. Over the past 20 years, there has been very little teaching at the university level about manufacturing operations. As companies moved manufacturing to China, there was no demand for manufacturing education. So we addressed this problem by hiring paid interns every semester. Our interns help us with research and sometimes with our consulting projects. We have a very big website where we post all of our research and everything is downloadable.
Cost savings have been the major driver of offshoring production. However, seeking low costs come with a price. What are the downsides and risks of business operations that involve worldwide long supply chains?
If you look at the total cost of ownership, particularly about the rising costs of logistics and rising labor costs around the world, you have to consider introducing automation to your production lines to make your operations more productive and cost-competitive. If you can extract labor out of production through automation, you can also achieve savings and become more cost-competitive. That is one factor to consider, but bringing manufacturing back home is not inexpensive.
Shutting down operations in foreign locations is often a difficult and costly process. You may have employment contracts, for example, where you have to pay the employees through the end of the contract period. You may have to request a permit to leave the foreign country. All these factors have to be taken into consideration.
There are many places and countries in the world where it is less expensive to manufacture, for example, Mexico and many places in Asia or India. But when you look at the total cost of ownership and reducing the length of your supply chains,
it often makes economic sense to manufacture close to your markets.
If your customers are in America, you should consider manufacturing there. I think this is the direction where we are now heading.
What factors other than costs would companies consider when they want to make production location decisions?
Now we are seeing policies and incentives by governments around the world, supporting local manufacturing. The pandemic exposed the risks of global supply chains and the need for manufacturing critical goods in your home country. The economic incentives for local manufacturing can be quite good. Most countries also have policies regarding buying preferences for domestically produced goods.
The outbreak of the coronavirus pandemic has led to significant disruption in various global supply chains. It suddenly revealed some of the underlying weaknesses and vulnerabilities of global supply chains. What, in your view, are the major lessons learned for businesses as well as for national policymakers?
The pandemic introduced risks into the supply chains. In the past we have focused mainly on costs - where in the world could you manufacture for the cheapest cost. However,
the pandemic revealed vulnerabilities throughout the supply chain.
Now, you would like to make sure that you have fundamental manufacturing capacity in your home country. For the U.S. that includes semiconductors, pharmaceuticals, and medical devices. These products are now at the forefront of manufacturing development in America and a lot of other countries.
From the US-China trade to the French president's aspirations we can also witness that protecting economic sovereignty is on the rise. How do you see these policies and their effects on supply chains?
That is an excellent question. Most countries around the world have developed industrial policies. They are promoting something or they are trying to protect their local industries in some way. It was a surprise to me when I found out that America has no industrial policy. For a long time, we have focused only on letting the markets determine what is being manufactured here. The pandemic exposed that idea as risky. I think we are going to see a policy initiative developed in America to determine industrial policies that protect certain industries. We know that certain industries are vulnerable such as pharmaceuticals. Pharmaceutical building blocks for many drugs such as antibiotics are made in China and India.
The U.S. has almost no production of these basic products.
So those are the products we are likely to see being produced in America in the future. Another category is rare earth elements. These are used in electronics, but there is practically no mining of rare earth elements in the U.S. We will likely see mining and refining rare earth elements develop in America.
You mentioned automation earlier in the conversation. How do you see the impacts of digitization and the rise of new technologies on supply chains realignment?
All kinds of automation whether it is 3D printing, IoT, advanced machine tools, or robotics are important when you look at the total cost of ownership. To make your manufacturing lines more efficient and to extract labor, you have to move towards an automated solution. This makes manufacturing competitive in high-cost areas like America. Therefore,
the move towards automation is critical.
It is one of the critical underpinnings of reshoring and looking at where in the world you should be manufacturing.
A lot of new terms have come to use such as “reshoring”, “nearshoring” or “right-shoring”. How do you see the perspective of this trend in the United States?
In my view, this is a gradual evolution. In today’s environment, it is an analytical and thoughtful process to determine where to manufacture. Should you bring back some manufacturing to the U.S. to meet the needs of the local markets? The same is true in Europe - should you bring back manufacturing to the U.K. or to France to serve these local markets? That is one trend. I think it is a maturing thought process also. There are manufacturing executives who are thinking differently about the global environment today.
Globalization is here to stay but must be better understood.
One of the things I think is not well-recognized is that we have a global economy. The global economy is very interdependent. It is impossible to survive as an isolated country. We are completely dependent on the global economy. Your manufacturing strategies need to reflect that as well.
If you take at Europe, how do you the position of the Central-European region in the European Union from this perspective? What policies should or could either the EU or countries in Central-European adopt to become the production powerhouse of Europe?
It is really important to start with cost structures because businesses make decisions based on economics. Businesses do not make decisions based on how they feel.
Central Europe can provide low-cost manufacturing areas and capabilities that are growing to serve the entire European market in the future and as an alternative to China.
I think we are going to see countries like France, Germany and the U.K. bringing their manufacturing back from China and locating new factories in countries of Central-Europe where the cost-structures are very competitive.
Besides the cost structure, what else do you think is important for this region to be competitive?
We have a current problem in the U.S. with labor shortages. We have a few million job openings but no workers with the right skills to fill the positions.
Addressing the problem of skilled labor is crucial.
The manufacturing work environment has changed due to digitization. For example, somebody needs to learn how to run a robot instead of doing the job of a robot. It is upskilling and retraining labor that is required now to fill the jobs available. The way to solve this challenge is through apprenticeships and technical training. We have to provide training to prepare manufacturing workers for the jobs currently available and for the future. There is no question we are rapidly moving towards digitization. The widespread introduction of new technologies is going forward fast.